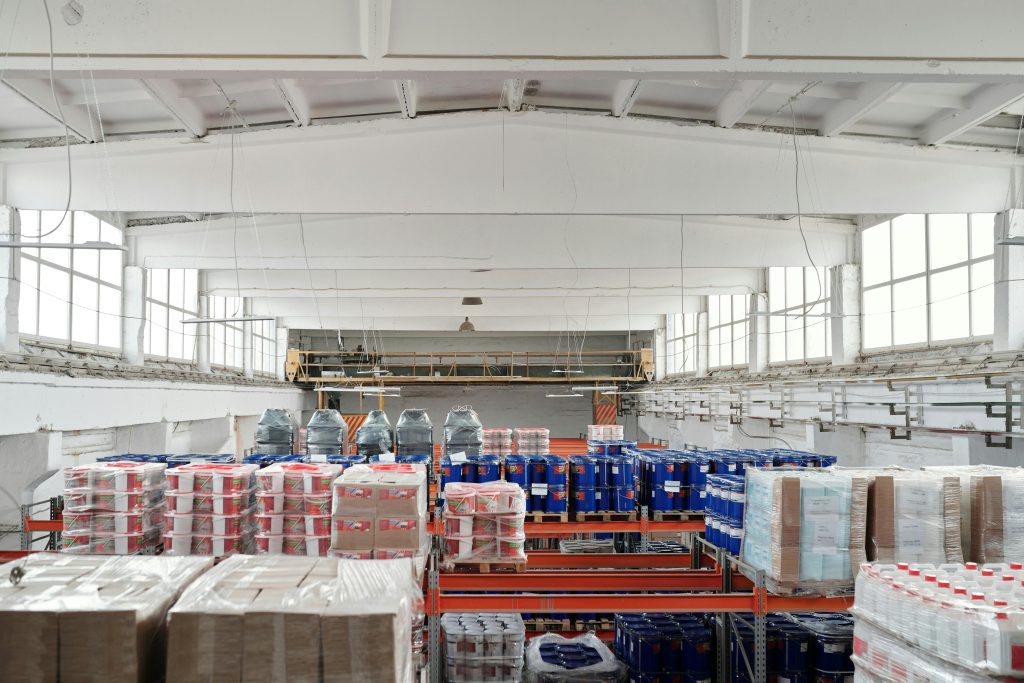
In inventory management, “warehouse” and “stockroom” are often used interchangeably, but they have distinct roles in efficient inventory management. Understanding their differences is essential for businesses aiming to streamline operations and optimize storage capabilities.
Definition and Purpose of a Warehouse
A warehouse is a large-scale facility that stores substantial quantities of goods for longer periods. It serves as a centralized hub for storing raw materials, finished products, or goods in transit before distribution or further processing. Warehouses are strategically located to facilitate efficient logistics and supply chain management, often integrating advanced technology for inventory tracking and management systems.
The primary purpose of a warehouse extends beyond storage; it includes facilitating order fulfillment, inventory control, and minimizing distribution costs. Warehouses are integral in managing fluctuating demand and ensuring timely deliveries to customers and retailers.
Definition and Purpose of a Stockroom
In contrast, a stockroom, sometimes referred to as a storeroom or storage area, is a smaller, localized space within a facility or retail establishment. It serves the immediate needs of day-to-day operations by storing frequently used items or supplies in close proximity to where they are needed. Stockrooms focus on quick access and retrieval, maintaining adequate levels of essential goods to support ongoing business activities.
The key purpose of a stockroom is to ensure operational continuity by keeping essential inventory readily available. Unlike warehouses, which handle large-scale storage and distribution, stockrooms cater to the immediate needs of production lines, retail shelves, or service provision.
Comparing Storage Capacities
One of the most notable differences between warehouses and stockrooms lies in their storage capacities. Warehouses accommodate vast quantities of goods, from pallets of products to entire shipping containers. They feature expansive floor space and often utilize vertical storage systems to maximize capacity.
On the other hand, stockrooms manage smaller volumes of inventory and have limited storage capacities. Their layout emphasizes accessibility and organization, with shelves, bins, or racks optimized for quick retrieval of items needed for daily operations.
Read more about calculating warehouse capacity.
Difference in Management and Operations
The management and operational dynamics of warehouses and stockrooms also differ significantly. Warehouse operations involve complex logistics, inventory tracking, and supply chain management systems. Warehouse managers oversee tasks such as receiving shipments, organizing inventory, maintaining stock levels, and coordinating outbound shipments.
In contrast, stockrooms operate on a smaller scale with a focus on maintaining inventory levels that support immediate operational needs. Stockroom management involves replenishing supplies, conducting regular inventory counts, ensuring stock accuracy, and optimizing space utilization within the confined area.
Related: Best Practices for a Smooth Supply Chain
Conclusion
In summary, while both warehouses and stockrooms play vital roles in inventory management, they serve distinct purposes and cater to different aspects of supply chain operations. Warehouses facilitate efficient logistics and inventory control across broader geographic areas by providing expansive facilities for large-scale storage and distribution. In contrast, stockrooms are localized storage areas within facilities or retail outlets, optimized for quick access and retrieval of essential goods to support daily operations.
Understanding these differences and leveraging each can boost inventory management, improve efficiency, and meet customer demands in a competitive market.